廢舊耐火材料制備再生顆粒料的新工藝
我國每年產(chǎn)生400多萬噸廢舊耐火材料,其中僅有20%得到簡單再利用,其余的作為工業(yè)垃圾被廢棄或掩埋[1],不僅浪費了資源,也污染了環(huán)境。以鋼鐵工業(yè)的高爐出鐵鉤主溝料、渣鐵溝料(含預制件)以及轉爐鋼包鎂碳磚為例,雖然含有電熔致密剛玉、電熔棕剛玉、電熔鎂砂和特級礬土等高檔耐火原料,但使用后往往只是經(jīng)過簡單破碎就直接使用在低檔耐火材料或冶金爐料中,附加值較低。
為了提高廢舊耐火材料的資源利用率和附加值,采用一種新工藝對使用后的主溝料、渣鐵溝料和鎂碳磚進行再生處理,制備了再生顆粒料,并用再生鎂碳顆粒料制成再生鎂碳磚在某大型鋼廠的鋼包渣線部位進行試用,效果較好。
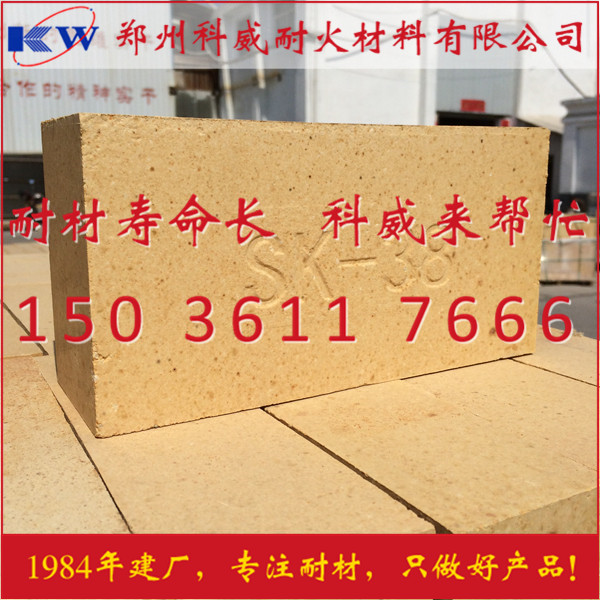
再生顆粒料工藝試驗
1.1廢舊耐火材料來源
本試驗中采用的廢舊耐火材料的來源有3種:一
是以電熔致密剛玉和高純碳化硅為主原料的高爐用后主溝料,二是以特級礬土、電熔棕剛玉和高純碳化硅為主原料的高爐用后渣鐵溝殘襯,三是轉爐鋼包包襯渣線部位的用后鎂碳磚。
1.2制備再生顆粒料的工藝流程
本試驗中采用新工藝對上述廢舊耐火材料進行
再生處理,主要工藝步驟如下:
(1)將混入用后主溝料中的渣鐵(約占用后主溝料質量的5%~10%)挑出;將用后渣鐵溝預制件表面的渣鐵(約占用后渣鐵溝預制件質量的30%)除去,并用沖擊鉆破碎;將用后轉爐鋼包鎂碳磚表面的渣鐵(約占用后鎂碳磚質量的5%~10%)去除。
(2)用PEX250×400型顎式破碎機將廢舊耐火材料破碎成<30mm的顆粒料。用后鎂碳顆粒料再進水化干燥窯進行水化分解和干燥,然后用對輥破碎機細碎到5mm以下。其他兩種用后顆粒料直接用對輥破碎機細碎到8mm以下。
(3)用SXG-260KL型顆粒整形機中整形20~45min。具體整形時間根據(jù)假顆粒的實際去除情況而定。
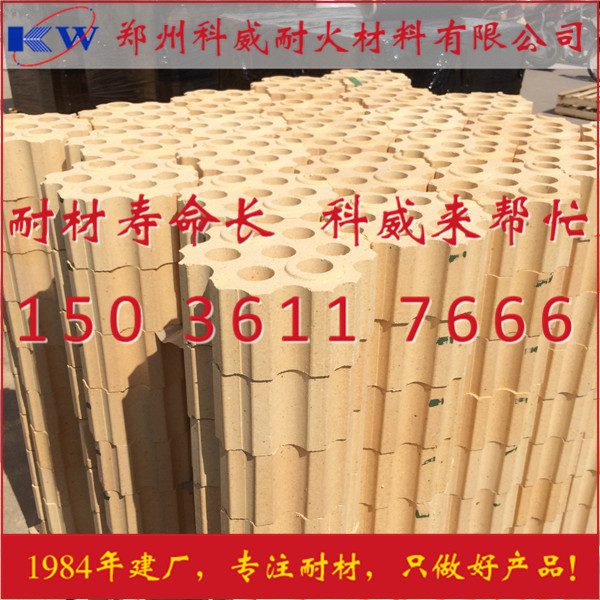
(4)將整形好的顆粒料用磁選機除鐵,然后根據(jù)其臨界顆粒的大小,用2ZD918型振動篩篩分,最后分析其化學組成。與傳統(tǒng)工藝相比,新工藝增加了水化干燥窯和顆粒整形設備,用后鎂碳顆粒經(jīng)水化干燥窯充分水化分解去除,再用顆粒整形機通過輪子的碾壓使廢舊中原始骨耐火材料料與基質分離,經(jīng)過篩分后即可獲得價值較高的再生顆粒料。
1.3制備再生顆粒料的工藝要點
采用新工藝對廢舊耐火材料進行再生處理時,要注意以下工藝要點:
(1)廢舊耐火材料加工前需人工分選和除雜,去除其中的冷鋼、大塊渣鐵和其他雜質,提高骨料的質量,并避免在加工過程中損傷設備。
(2)顆粒整形機的選擇。顆粒整形機輪碾壓力過大,容易破壞骨料顆粒;輪碾壓力過小,碾壓效果不明顯。碾輪上須有升降彈簧,可根據(jù)物料高度自動調節(jié)碾輪高度。建議購買專業(yè)的顆粒整形設備。
(3)整形時間的控制。整形時間太短,原始骨料與基質不能有效分離,“假顆粒”較多;整形時間太長,原始骨料也會被碾碎,利用價值降低。
(4)磁選工藝。應選擇磁選效果較好的中強磁設備,最好選用雙滾磁選機;上下滾筒表面場強匹配要合理,必要時可重復磁選過程。
1.4結果與分析
1.4.1再生顆粒料的形貌
采用傳統(tǒng)工藝與新工藝制備的再生顆粒料的形貌可以看出,采用傳統(tǒng)工藝制得的再生顆粒料,其原始骨料與基質層部分不能有效分離,屬于“假顆粒”。采用新工藝制得的再生顆粒料粒形棱角較分明,與原始骨料相似,表明廢舊耐火材料中的原始骨料與基質分離較好。除了再生顆粒料的品質提升以外,新工藝還使三種廢舊耐火材料骨料的收得率分別提高了3~5百分點。
1.4.2再生顆粒料的粒度組成
采用新工藝制得的三種再生顆粒料的粒度組成。可知,再生顆粒料的粒度大部分集中在5~1mm,這與生產(chǎn)制品所需的原料粒度基本相符。
1.4.3再生顆粒料的化學組成
再生剛玉顆粒料、再生礬土顆粒料和再生鎂碳顆粒料的化學組成可以看出采用新工藝制備的再生顆粒料的化學組成更加接近原生料的水平。
2再生顆粒料的應用
加入60%(w)再生鎂碳顆粒料制成了再生鎂碳磚,在某大型鋼廠轉爐鋼包渣線部位(砌筑了3環(huán))使用93次下線中修,未出現(xiàn)剝落和異常熔損等情況,使用效果與非再生鎂碳磚相當。
3結論
采用新工藝處理廢舊耐火材料制備的再生顆粒料品質較好,完全可以滿足生產(chǎn)使用,在生產(chǎn)應用中效果良好。制備再生顆粒料的新工藝采用流水線作業(yè),簡單實用,勞動強度低,生產(chǎn)效率高,環(huán)境污染小,能耗低。
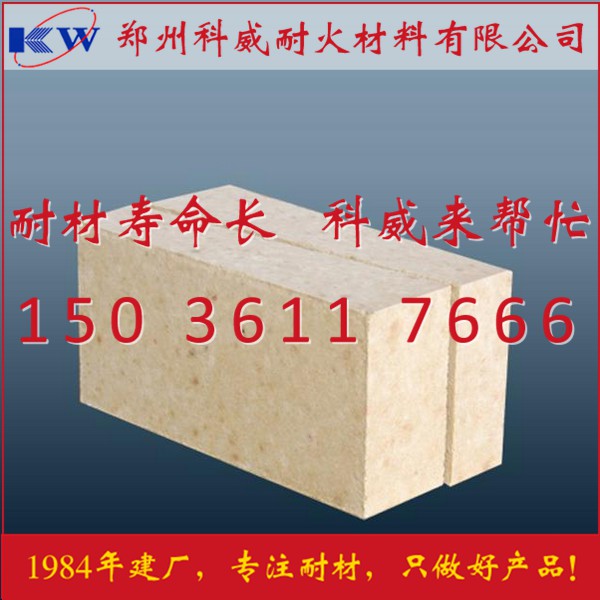